Exploring Continuous Operation of Automated Tray Formers — Manufacturer Insights and Operational Str
2025-04-25
Exploring Continuous Operation of Automated Tray Formers — Manufacturer Insights and Operational Strategies
The ability of an automated tray former to operate continuously without interruption is a frequent concern among users and buyers. Responses may vary across manufacturers; however, top-tier manufacturers typically back their equipment with advanced engineering and robust technical support, ensuring high uptime and reliable performance during extended operation.
1. Design and Technical Features Supporting Continuous Operation
Reputable manufacturers equip their tray formers with features that specifically support long-term, uninterrupted use:
Servo-Driven Systems: Servo motors provide precise motion control, reducing mechanical wear and increasing consistency in tray forming.
Quick-Change Tooling (Modular Design): Allows for fast changeover between tray sizes or designs, minimizing downtime during production shifts.
Automatic Lubrication and Maintenance Alerts: These systems prolong mechanical life and reduce the need for manual intervention.
Sensor Integration and Error Detection: Optical or inductive sensors detect misfeeds, tray jams, or blank shortages in real time, triggering alarms and auto-stops to prevent damage.
Smart PLC and HMI Interfaces: Programmable logic controllers with user-friendly touch screens allow real-time monitoring, parameter adjustments, and diagnostics.
2. Strategic Planning for Continuous Use
To run an automated tray former in continuous cycles (24/7 or multiple shifts), a comprehensive operational strategy is essential. Key aspects include:
Preventive Maintenance Schedules: Establish routine checks and scheduled stops to inspect wear parts (e.g., forming mandrels, suction cups, guide rails).
Training for Operators: Reducing human error through thorough training on machine setup, operation, and emergency procedures.
Spare Parts Readiness: Maintain inventory of critical consumables such as vacuum cups, belts, sensors, and control modules.
Real-Time Monitoring and Data Logging: Advanced models offer production data analytics, allowing predictive maintenance and efficiency tracking.
3. Manufacturer Support and Operational Insights
Leading manufacturers not only provide machines capable of reliable continuous operation but also offer dedicated technical teams who respond quickly to breakdowns or maintenance needs. Remote diagnostics and online support have become increasingly common, minimizing production delays.
It’s important to understand that while machines may technically support continuous operation, real-world efficiency relies on how well-prepared the user is. Even with 24-hour staffing, without a proper response plan for issues such as blank feeding errors, glue nozzle blockages, or misalignment, unexpected downtime can occur.
4. Conclusion: Proactive Is Better Than Reactive
Ultimately, achieving truly continuous operation depends not just on the quality of the equipment, but on a proactive and systematic operational approach. This includes identifying potential failure points, planning preventive measures, and working closely with the manufacturer for technical guidance.
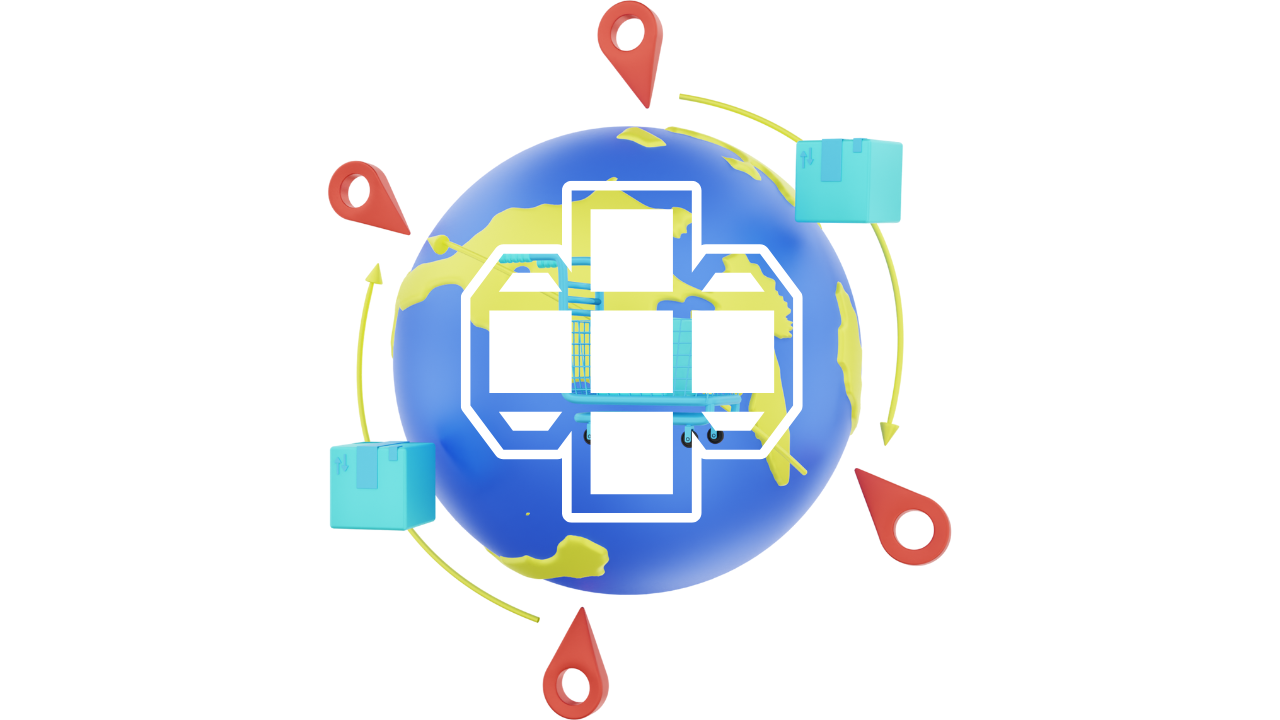